How can IoT help tool manufacturing companies?
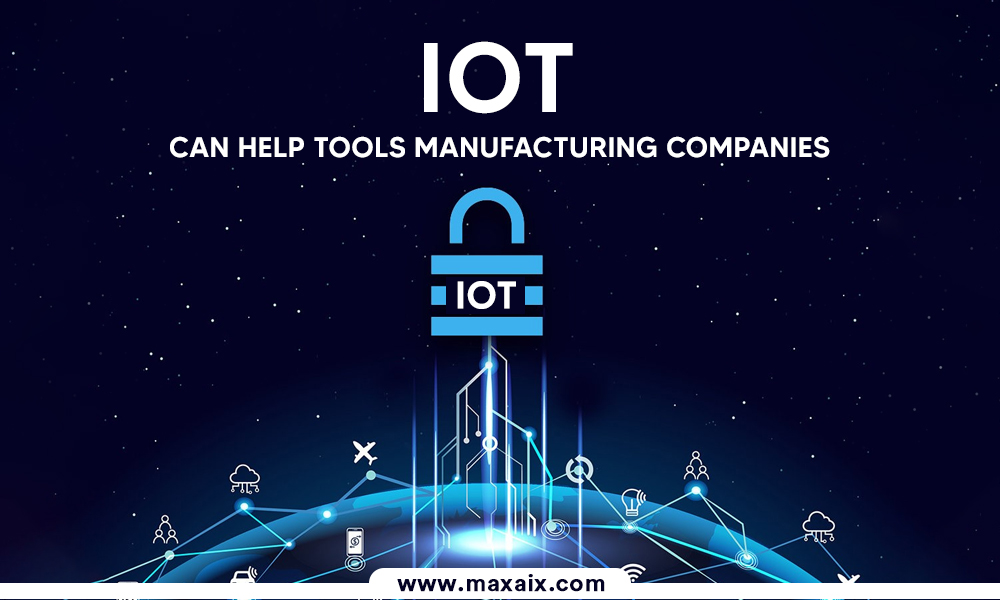
The Internet of Things (IoT) is revolutionizing diverse industries, and tool manufacturing isn’t an exception. This article explores how the IoT can help tool manufacturing groups beautify their operations, improve performance, and take advantage of an aggressive side. We’ll cover the fundamentals of IoT, its impact on manufacturing, the primary advantages for tool manufacturers, realistic use cases, challenges, solutions, and much more.
What is IoT?
The Internet of Things (IoT) refers to the interconnected network of devices that talk and exchange records over the Internet. These devices, or “matters,” are embedded with sensors, software, and different technologies that permit them to gather and transmit facts, bearing in mind sensible decision-making and automation.
Key Components of the IoT
- Sensors and actuators: Devices that accumulate records from the environment or perform movements primarily based on commands.
- Data Processing:Connectivity: Communication protocols that enable gadgets to connect and percentage facts.
- Data Processing: Systems that examine and mannerly gather data to derive significant insights.
- User Interface: Platforms that permit customers to interact with and manage IoT devices.
Applications of the IoT
- Smart Homes: connected appliances, lights, and safety systems.
- Healthcare: Remote patient tracking and smart scientific gadgets.
- Transportation: Fleet control and autonomous motors.
- Manufacturing: Industrial automation and predictive preservation.
How IoT Works
IoT gadgets accumulate information from their surroundings via sensors. This record is transmitted via connectivity protocols to an imperative system, where it’s processed and analyzed. The insights derived from this evaluation can trigger moves, together with adjusting machinery settings or sending indicators to protection groups. This seamless glide of information and movement is the backbone of IoT functionality.
IoT in Tool Manufacturing Companies
Tool production companies are increasingly adopting IoT to streamline their operations, enhance product quality, and enhance purchaser satisfaction. IoT allows these agencies to connect their machinery, equipment, and systems, creating a smart manufacturing environment.
The Role of IoT in Manufacturing
IoT performs a pivotal function within the digital transformation of the manufacturing enterprise. It allows real-time tracking, predictive protection, and optimized production methods. For tool manufacturing corporations, IoT can considerably improve operational performance and product quality.
Integration of IoT in Tool Manufacturing
- Smart Machinery: IoT-enabled machines that can screen their own overall performance and document troubles.
- Connected Tools: Tools equipped with sensors that offer real-time data on utilization and put-on.
- Automated Production Lines: Systems that automate various stages of the production method using IoT.
Objectives of IoT Adoption
- Efficiency: Reducing downtime and optimizing aid usage.
- Quality: Enhancing product quality through better monitoring and management.
- Innovation: Enabling new commercial enterprise models and offerings through connected products.
The Impact of IoT on Manufacturing Companies
IoT has a profound impact on manufacturing agencies, transforming how they perform and compete within the marketplace. By leveraging IoT, producers can acquire better performance, reduce charges, and innovate their product services.
Operational Efficiency
- Real-Time Monitoring: Continuous tracking of machinery and manufacturing approaches to detect and cope with troubles right away.
- Predictive Maintenance: Using data analytics to expect and save your gadget disasters before they arise.
- Resource Optimization: Better usage of materials, electricity, and labor through facts-pushed insights.
Cost Reduction
- Lower Maintenance Costs: Reducing unplanned downtime and restoring fees through predictive protection.
- Energy Savings: Optimizing Strength Intake in Manufacturing Tactics.
- Reduced Waste: Minimizing fabric waste through specific tracking and manipulation.
Product Innovation
- Smart Products: Developing related gear that offers improved functionality and the consumer experience.
- New Business Models: Offering services consisting of faraway diagnostics and predictive upkeep to customers.
- Customization: Enabling mass customization through flexible and responsive production tactics.
What are the main benefits of IoT for tool manufacturing companies?
Tool production companies can gain several benefits from adopting IoT, starting with improved performance and better client pride.
Enhanced Efficiency
- Automated Operations: Automating repetitive tasks and approaches to reduce human error and increase productivity.
- Real-Time Data: Access to actual-time facts for better selection-making and quicker response to problems.
- Optimized Workflows: Streamlining workflows and reducing bottlenecks via information-driven insights.
Improved Product Quality
- Quality Control: continuous monitoring of manufacturing techniques to ensure steady product quality.
- Traceability: tracking the entire manufacturing lifecycle to discover and cope with exceptional issues.
- Customer Feedback: Using IoT facts to understand patron utilization and preferences for non-stop improvement.
Cost Savings
- Maintenance: Predictive protection to keep away from luxurious breakdowns and enlarged gadget lifestyles.
- Energy Management: Reducing energy consumption via optimized operations.
- Inventory Management: Better inventory manipulation to reduce excess inventory and associated fees.
Customer Satisfaction
- Responsive Service: Providing well-timed and proactive customer support through linked merchandise.
- Customized Solutions: Offering personalized services and products based totally on customer statistics.
- Enhanced Experience: Improving the overall patron experience through clever and connected equipment.
IoT Use Cases in Manufacturing: From Product to Service
IoT enables an extensive range of use instances in manufacturing, reworking both products and services. Here are a few realistic examples:
Smart Manufacturing
- Automated Production Lines: IoT permits the automation of production lines, lowering human intervention and increasing efficiency.
- Real-Time Monitoring: Sensors and connected gadgets display production tactics in real-time, ensuring optimal performance and high-quality management.
- Predictive Maintenance: IoT structures analyze records from machinery to anticipate failures and schedule renovations proactively.
Connected Tools
- Tool Tracking: IoT-enabled equipment can be tracked in real-time, making sure it is usually available when needed and lowering losses.
- Usage Monitoring: Sensors embedded in tools provide statistics on utilization styles, helping to optimize device performance and lifespan.
- Remote Diagnostics: Connected tools can ship diagnostic data to manufacturers, permitting far-off troubleshooting and support.
Smart Products
- Enhanced Functionality: IoT permits the improvement of clever equipment with advanced functions, including automated modifications and condition monitoring.
- Customer Insights: Connected merchandise offers precious records on purchaser usage and alternatives, permitting manufacturers to improve their offerings.
- Value-Added Services: Manufacturers can provide extra offerings, including far-flung monitoring and predictive renovation, improving the cost of their products.
Digital Twins
- Virtual Replicas: Creating digital twins of manufacturing approaches and systems to simulate and optimize operations.
- Performance Analysis: Using digital twins to analyze performance information and discover regions for improvement.
- Scenario testing: Testing exclusive situations and changes in a digital environment before imposing them on the actual world.
How Does IoT Help Tool Manufacturing Companies?
IoT allows tool production businesses numerous approaches, from improving operational performance to enhancing purchaser pride. Here are a few key benefits:
Real-Time Data Collection and Analysis
- Continuous Monitoring: IoT gadgets collect statistics continuously, offering actual-time insights into manufacturing tactics.
- Data Analytics: Analyzing statistics to identify trends, patterns, and anomalies, permitting informed selection-making.
- Performance Optimization: Using records to optimize device’s overall performance and manufacturing methods.
Predictive Maintenance
- Failure Prediction: Using information analytics to expect capability gadget disasters earlier than they occur.
- Scheduled Maintenance: Scheduling preservation sports based on predictive insights reduces unplanned downtime.
- Cost Savings: Reducing renovation charges and extending equipment lifespan through proactive renovation.
Enhanced Quality Control
- Quality Monitoring: Monitoring manufacturing strategies in real-time to ensure constant product quality.
- Defect Detection: Using sensors and record analytics to stumble on defects early within the production procedure.
- Continuous Improvement: Analyzing quality records to pick out areas for improvement and put corrective actions into effect.
Supply Chain Optimization
- Inventory Management: Optimizing inventory ranges through actual time tracking and fact evaluation.
- Demand Forecasting: Using IoT records to forecast demand as it should be and regulate manufacturing for that reason.
- Logistics Management: Improving logistics and transportation through real-time monitoring and optimization.
Customer Engagement
- Connected Products: Developing smart tools that provide more suitable functionality and that consumers enjoy.
- Remote Support: Offering faraway diagnostics and help through linked products.
- Customer Feedback: Collecting and analyzing purchaser utilization statistics to enhance services and products.
IoT Challenges and Solutions in Manufacturing
While IoT offers several benefits, it additionally presents numerous challenges that manufacturers should deal with to understand its capacity completely.
Data Security and Privacy
Challenge: Protecting touchy records from cyber threats and ensuring user privacy.
Solution: Implementing sturdy safety features, including encryption, stable authentication, and regular protection audits.
Integration with Legacy Systems
Challenge: Integrating IoT solutions with present legacy systems and infrastructure.
Solution: Using middleware and APIs to facilitate integration and ensure seamless verbal exchange between structures.
Scalability
Challenge: Ensuring that IoT answers can scale to deal with growing statistics volumes and device numbers.
Solution: Designing scalable architectures and the usage of cloud-based platforms to handle multiplied information and device loads.
Data Management
Challenge: Managing and analyzing huge volumes of statistics generated by IoT devices.
Solution: Implementing superior statistics analytics tools and systems to process and derive insights from IoT statistics.
Interoperability
Challenge: Ensuring that different IoT gadgets and systems can talk and work collectively correctly.
Solution: Adopting open requirements and protocols to ensure interoperability and compatibility between gadgets.
Cost
Challenge: The preliminary investment required for enforcing IoT solutions can be substantial.
Solution: Demonstrating the long-term ROI and value savings to justify the funding and exploring financing alternatives.
IoT Application Development Services – Maxaix
Maxaix is a leading provider of IoT application development services, specializing in creating innovative and scalable IoT solutions for various industries, including manufacturing. With a team of experienced developers and a proven track record of successful projects, Maxaix helps businesses leverage IoT technology to drive efficiency, improve product quality, and enhance customer satisfaction.
Services Offered
- IoT Consulting: Expert consulting services to help businesses develop a comprehensive IoT strategy and roadmap.
- Custom IoT Application Development: Tailored IoT solutions designed to meet each client’s specific needs and requirements.
- IoT Integration: Seamless integration of IoT devices and systems with existing enterprise applications and infrastructure.
- Data Analytics: Advanced data analytics and visualization tools to derive actionable insights from IoT data.
- Maintenance and Support: Ongoing maintenance and support services to ensure the smooth operation of IoT solutions.
Benefits of Partnering with Maxaix
- Expertise: A team of skilled developers with extensive experience in IoT application development.
- Innovation: Cutting-edge technology and innovative solutions that drive business growth and efficiency.
- Scalability: Scalable IoT solutions that can grow with your business and adapt to changing needs.
- Cost-Effective: Competitive pricing and flexible engagement models to suit various budgets and requirements.
- Customer Satisfaction: A commitment to delivering high-quality solutions that meet and exceed client expectations.
Conclusion
IoT is reworking the device manufacturing enterprise by allowing smarter, more efficient, and more innovative operations. By adopting IoT, tool producers can improve their operational efficiency, enhance product quality, reduce fees, and provide new fee-delivered services to clients. While there are demanding situations to triumph over, the blessings of IoT in production far outweigh the risks, making it an essential era for the future of the enterprise.
Frequently Asked Questions
- How can IoT enhance operational efficiency in device manufacturing?
IoT improves operational performance by allowing real-time monitoring, predictive protection, and record-driven decision-making. It enables optimization of workflows, lessens downtime, and beautifies useful resource usage. - What are the main blessings of IoT for tool production corporations?
The foremost blessings include greater efficiency, advanced product satisfaction, price savings, and elevated patron satisfaction. The IoT permits automated operations, better first-class control, predictive protection, and clever merchandise. - How does IoT enable predictive protection in production?
IoT allows predictive renovation through sensors and records analytics to monitor device performance and expect capacity failures. This permits proactive renovation, reducing unplanned downtime, and restoring prices. - What challenges do device manufacturing organizations face while implementing IoT?
Challenges include data protection and privacy, integration with legacy systems, scalability, information control, interoperability, and price. Addressing those demanding situations requires strong security measures, scalable architectures, and superior information analytics gear. - How can IoT enhance client engagement for tool producers?
IoT enhances customer engagement by allowing related merchandise with advanced features, far-off support, and customer remarks series. This permits manufacturers to provide personalized services and products and enhance the standard client experience. - What is the position of information analytics in IoT for device production?
Data analytics plays a vital function in IoT by processing and analyzing the huge volumes of statistics generated by IoT devices. It enables individuals to derive significant insights, optimize overall performance, and assist in informed choice-making. - How can device manufacturing groups justify the funding for IoT?
Companies can justify their funding in IoT by demonstrating the long-term ROI and fee-based financial savings. IoT improves efficiency, reduces charges, enhances product quality, and allows for new revenue streams, making it worthwhile for funding in the future.